Hersteller von Verpackungen können in ihrem Beschichtungsbereich an mehreren Stellen Brände erleiden, die durch Funken hoher statischer Aufladung verursacht werden. Betreiber, die mit diesem Problem konfrontiert werden, benötigen industrielle antistatische Lösungen, um dieses Problem zu lösen.
Je nach Abstand zum Material kann in jedem Maschinenabschnitt der Einsatz unterschiedlicher
Ionisationsstäbe erforderlich sein. Auch verschiedene Arten von Walzen, durch die das Material läuft,
beeinflussen die statische Aufladung der Bahn. Besondere Aufmerksamkeit für die Sicherheit ist
erforderlich, wenn es sich um den Ex-Bereich handelt, wo ausschließlich der Einsatz ATEX-zertifizierter
Entladestäbe zulässig ist.
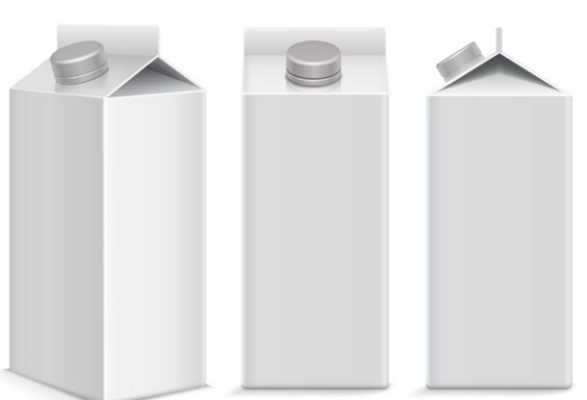
Um genau zu erfahren wo die statische Aufladung erzeugt wird und eine Entladung erforderlich ist, müssen verschiedene Messungen durchgeführt werden. Zur Messung der genauen statischen Aufladung wird ein FMX-Handmessgerät oder eine IQ-Sensorleiste für die Inline-Messung empfohlen.
Das Abwickeln von Kunststofffolien kann statische Aufladungen von bis zu 20 kV oder mehr verursachen, und die Bahn muss direkt nach dem Abwickeln neutralisiert werden. Durch die Installation eines
Hochleistungsentladestabes wird auch verhindert, dass statische Aufladung Staubpartikel anzieht.
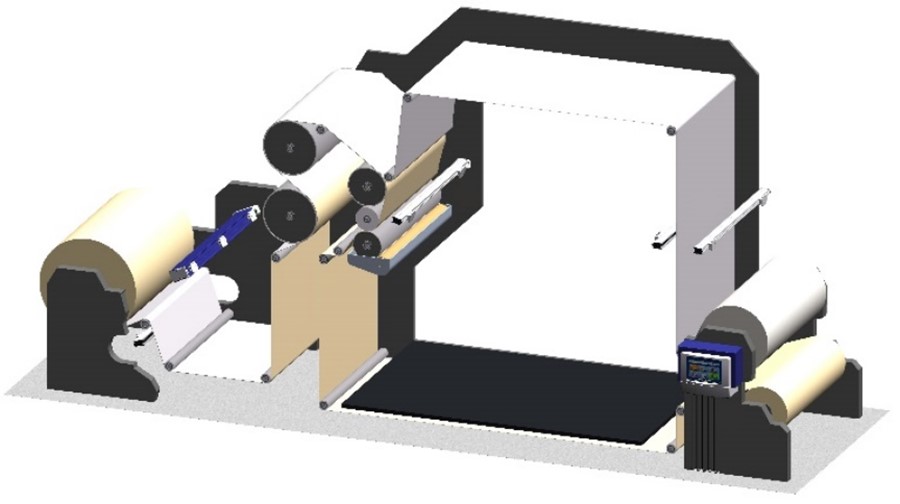
Wenn das Material eine Korona-Vorbehandlung passiert, wird eine massive statische Aufladung des
Materials erzeugt und ein geregeltes Entladesystem (in Close Loop Feedback; CLFB) wird empfohlen.
Bevor das Material in den Beschichter (ATEX-Zone) gelangt, müssen beide Seiten des Materials
entladen werden, um zu verhindern, dass die vorhandene statische Aufladung als mögliche Zündquelle
fungiert, die zu einem Brand führen kann.
Innerhalb des Coaters passiert das Material mehrere Walzen und es entsteht eine statische Aufladung.
ATEX-zertifizierte Ionisationsstäbe neutralisieren die statische Aufladung auf beiden Seiten der Bahn, um zu verhindern, dass statische Aufladung als mögliche Zündquelle fungiert. Das Verschmutzungs- und
Effizienzniveau wird vom IQ-Manager überwacht. Wenn die Effektivität unter ein vorprogrammiertes Niveau fällt, erhält die SPS oder der Bediener eine Warnung, damit er die angezeigten Ionisationsstäbe warten kann.
Während des Trocknungsprozesses kann sich das Material aufgrund der Temperaturschwankungen im Trockner wieder aufladen. Hier und auch vor dem Laminierungsprozess neutralisieren 24-V-Ionisationsstäbe die Bahn und verhindern, dass die statische Aufladung zwischen den Schichten eingeschlossen wird.
Beim Aufwickler kann am Material aufgrund der Andruckwalzen erneut hohe statische Aufladungen erzeugt werden, was dazu führt, dass der Bediener in der Nähe des Materials Stromschläge bekommen kann. Da sich, besonders im Wendewickler, der Abstand des Entladestabes zum Material ändert, ist ein
ThunderIon-Entladestab erforderlich, um die statischen Ladungen, die beim endgültigen Wickeln entstehen, wirksam zu beseitigen.
Zusätzliche Anforderungen hinsichtlich der statischen Ladung oder der Gewährleistung der Personensicherheit können mit dem IQ Manager System mit statischer Inline-Messung und Closed-Loop-Feedback-Technologie erfüllt werden.
Der IQ Manager kann über eine Feldbusverbindung direkt an die Maschinen-SPS angeschlossen werden. Eine Alarmfunktion warnt den Bediener, falls die statische Aufladung eine gefährliche Stufe erreicht. Inline-Messung und Datenerfassung von statischen Ladungspegeln können in der Qualitätsberichterstattung verwendet werden. Auf diese Weise liefert das Manager IQ-System alle wichtigen Informationen, um die Sicherheit des Personals zu erhöhen und die Wahrscheinlichkeit neuer Brände auf ein Minimum zu reduzieren.
Möchten Sie mehr über die Wirkung statischer Elektrizität erfahren?
Dann laden Sie sich direkt von unserer Startseite unser Handbuch „Elektrostatik in der Produktion“ mit 5 weiteren konkreten Anwendungsfällen herunter.